Introduction to 589r112g01 Wire Wrap Board
For many years, wire wrapping has been the preferred technique for creating electronic circuits because of its accuracy, robustness, and dependability. Learning this method can lead to a plethora of opportunities, regardless of your level of experience with electronics.
The 589r112g01 wire wrap board, which is at the heart of this craft, is a strong and adaptable instrument that facilitates and expedites circuit assembly. This tutorial offers everything you need whether you are unsure about where to begin or want to hone your abilities!
We will cover all you need to know in this blog, from the fundamentals of wire wrapping to the reasons the 589r112g01 board is revolutionary. We will also provide helpful hints and enjoyable project suggestions to help you get the most out of this method. Prepare to explore the realm of wire wrapping and realize your circuit designs!
The Basics of the 589R112G01 Wire Wrap Board
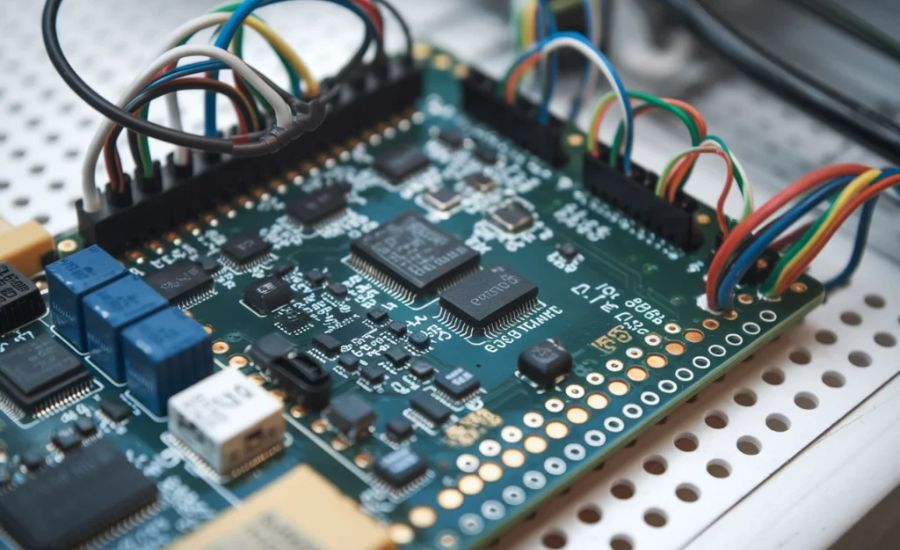
Electrical connections can be easily made without the trouble of soldering thanks to the 589R112G01 wire wrap board. This technique, known as wire wrapping, creates a strong electrical link by tightly wrapping a wire around a terminal rather than utilizing heat and solder. Wire wrapping, which is renowned for its dependability and durability, frequently performs better than traditional soldering, particularly in circumstances that call for flexibility and strong connections.
With its grid-like terminal structure, this board offers users a flexible area to easily develop and change circuits. Reconfiguring connections rapidly is one of its greatest benefits. Wire-wrapped connections are easily undone by simply unwrapping and rewrapping the wire, in contrast to soldered junctions, which are permanent and need desoldering for adjustments. Because of this, it is the perfect option for prototyping, which calls for regular modifications and iterative design enhancements.
The 589R112G01 wire wrap board offers a stable and versatile foundation for creating and testing circuits, regardless of your background as an engineer, maker, or electronics hobbyist. Because of its versatility, dependability, and user-friendliness, it is the preferred tool for anyone wishing to efficiently develop and improve electronic designs.
Exploring the Essence: What is the 589R112G01 Wire Wrap Board?
For engineers and technicians working on electronic circuit prototypes, the 589R112G01 Wire Wrap Board is an essential tool. It offers a precise and adaptable method of manually joining parts, which facilitates testing and design modification without the need for soldering. The board is a vital tool in the development process because of its hands-on approach, which enables fast alterations and dependable connections.
Real-World Applications and Project Ideas
For electronics aficionados, the 589R112G01 Wire Wrap Board is revolutionary since it provides countless opportunities for imaginative ideas. The following suggestions will help you get inspired:
Personalized Audio Amplifiers
Create a small, powerful amplifier for music enthusiasts. Wire wrapping makes it simple to adjust the circuit to produce the ideal sound.
Microcontroller Development
Develop and test smart devices, ranging from robotics and automation systems to Internet of Things devices, by experimenting with microcontrollers such as Arduino or PIC.
Electronic Displays
Building LED matrix displays or other visually striking projects with the board is a great way to learn about digital communication and display technology.
Systems Based on Sensors
Create an environmental monitoring system or other intelligent applications by integrating sensors, such as motion, temperature, or humidity detectors.
The 589R112G01’s adaptability and simplicity of use make it a vital instrument for realizing your electronic concepts!
Technical Specifications
The 589R112G01 Wire Wrap Board is a dependable option for electronic circuit design since it is constructed with accuracy and longevity in mind. Usually, premium materials like fiberglass or phenolic resin—both renowned for their superior mechanical strength and electrical insulation—are used to make it. The board’s terminals are frequently covered with protective metals like tin or gold to increase durability and stop corrosion.
For circuits with a large number of connection points, each terminal is specifically made to accommodate multiple wire connections. To ensure a secure connection, a segment of exposed insulated wire is gently wound around the terminal using the wire wrapping technique. In addition to offering stability, this technique keeps nearby wires safe and insulated, which helps avoid short circuits.
Efficient handling of high-frequency signals is one of the 589R112G01’s most notable characteristics. A steady, low-impedance channel is maintained by wire wrapping as opposed to soldered connections, which may cause interference or signal loss. Because of this, it is the ideal option for applications that need accuracy and fast performance, guaranteeing dependability in even the most taxing electronic projects.
The Future of Wire Wrapping Technology
Although soldering is still the most common method for mass-producing PCBs, wire wrapping is becoming more popular in specialized applications and prototyping. Because of its adaptability, durability, and simplicity of modification, the 589R112G01 Wire Wrap Board is quickly becoming a preferred tool among electronics enthusiasts.
Future developments in equipment and materials may make wire wrapping even more useful and effective. This technology may advance with innovations that reduce costs, enhance sustainability, and incorporate automation, enhancing its position in electronics development and enhancing contemporary circuit design techniques.
Applications of the 589R112G01 Wire Wrap Board
Due to its great versatility, the 589R112G01 Wire Wrap Board is used in many different sectors. Wire wrap boards were crucial for creating and testing large-scale mainframe systems in the early days of computers. For the trailblazing technologists who were creating the foundation for modern computing systems, these boards were essential.
The 589R112G01 is still in widespread usage today in vital industries like industrial automation, telecommunications, and aerospace. Circuit board performance and dependability are critical in aerospace, particularly for avionics and control systems. The robust wire-wrapped connections are ideal for the exacting specifications of aerospace applications because they withstand harsh environments including vibrations and extremely high or low temperatures.
The board is utilized in network infrastructure and signal processing in telecommunications, guaranteeing little distortion and great signal integrity even while working with high-frequency transmissions. The 589R112G01 is also essential for designing and adjusting circuits for programmable logic controllers (PLCs) and other control systems in industrial automation. It is a priceless instrument for creating dependable, effective circuits for automation processes because of its adaptability and simplicity of use.
Manufacturing Process of the 589R112G01 Wire Wrap Board
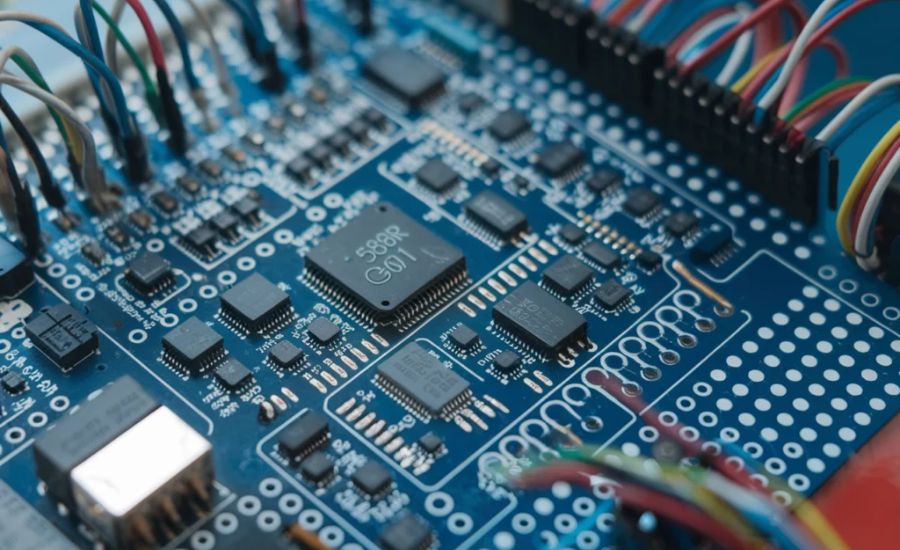
The 589R112G01 Wire Wrap Board’s production process is meticulously planned to guarantee its dependability and excellent performance. The base material is first cut and shaped to the necessary measurements. Then, in order to facilitate the smooth construction of circuits, precise holes are drilled into the board at regular intervals in a grid pattern.
After that, sturdy terminals are put into the holes that have been bored and fastened firmly. The high-conductivity metals used to make these terminals were picked for their durability. They are frequently coated with corrosion-resistant elements like tin, silver, or gold to increase their endurance and guarantee the board’s dependability over time.
The board is put through a rigorous testing process to confirm its mechanical and electrical characteristics after the terminals are installed. To satisfy the exacting requirements needed for professional applications, every terminal is meticulously examined for correct alignment and conductivity. The 589R112G01 Wire Wrap Board is meticulously packaged and sent to clients all over the world after passing rigorous quality tests.
The 589R112G01 Wire Wrap Board is a crucial component in prototyping. During this stage, engineers frequently need to test out various circuit designs, so having a platform that is both flexible and adaptive is essential. Engineers can swiftly create and modify circuits thanks to the wire wrap board’s straightforward adjustments that eliminate the need for soldering. This saves time and money by streamlining and improving the prototyping process.
Decoding the Core: Key Features of the Wire Wrap Board
Design and Durability
The 589R112G01 Wire Wrap Board is well renowned for its robust construction and capacity to withstand numerous alterations without compromising the integrity of the circuit. It is perfect for testing and fine-tuning circuit designs prior to final production because of its thoughtfully designed layout, which can accommodate intricate wiring arrangements.
Versatility and Compatibility
The board provides the versatility required for prototyping various electronic device types since it is compatible with a wide range of components and supports varying wire gauges. This adaptability is necessary to produce a variety of unique projects.
Technical Deep Dive: Specifications and More
The 589R112G01 Wire Wrap Board has a robust base that can support a broad range of electrical components because it was made with longevity and adaptability in mind. It is a user-friendly option for circuit design and prototyping because of its optimized size, which guarantees effective use of workspace while providing simple access for wiring and changes.
Performance of Electrical Systems
Constructed to facilitate a broad spectrum of prototyping endeavors, the 589R112G01 functions within a voltage range that accommodates numerous electronic systems. It ensures the seamless integration of different components for the construction of efficient, working circuits by providing dependable conductivity with low resistance.
Resilience in the Environment
This wire wrap board is designed to endure a range of environmental circumstances. Despite variations in humidity and temperature, it operates dependably, preserving the integrity of its parts and guaranteeing steady performance. This makes it a reliable choice for field applications as well as laboratory settings.
Looking Ahead: The Future of Wire Wrap Technology
Improvements in wire wrap boards are possible as technology advances. With prospective future improvements that will enable it to satisfy the expanding demands of the IT sector, the 589R112G01 is built to adapt to new trends and developments. The board will remain a useful tool for engineers and hobbyists for many years to come thanks to this continuous improvement.
Methods of Strategic Wiring
It is crucial to properly plan your layout and arrange the wires before beginning in order to build circuits that are efficient and seamless. Each link should be clearly labeled to prevent misunderstanding, improve process efficiency, and lower the possibility of mistakes.
Frequent Upkeep
For the board to last a long time and function at its best, maintenance is necessary. Develop the routine of cleaning the board’s surface, looking for any possible short circuits, and checking for loose connections. Frequent maintenance avoids problems later on and helps guarantee a seamless prototyping process.
Making Use of Modular Parts
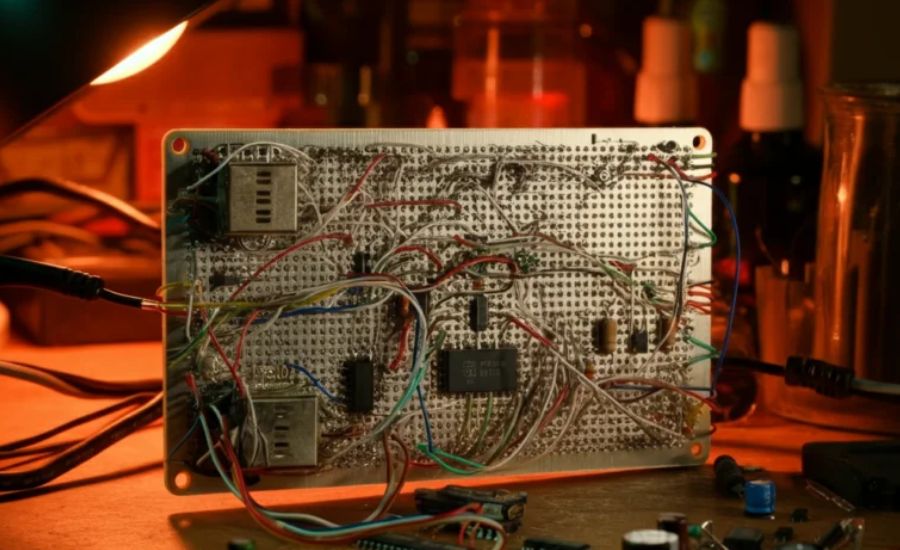
Whenever feasible, use modular components when creating circuits. As your project develops and expands, this method offers more flexibility by enabling simple updates or tweaks without requiring a whole setup overhaul.
Facts:
- Wire Wrapping Technique: The 589R112G01 Wire Wrap Board uses the wire wrapping method, which involves wrapping an insulated wire around a terminal to create a strong electrical connection. Unlike soldering, this method offers flexibility and reliability, especially for prototyping and high-frequency applications.
- Materials and Durability: The board is constructed from high-quality materials like fiberglass or phenolic resin, providing excellent electrical insulation and mechanical strength. The terminals are often coated with corrosion-resistant metals like tin, silver, or gold for enhanced durability.
- Applications Across Industries: The 589R112G01 is used in aerospace, telecommunications, industrial automation, and more. Its robust design makes it ideal for harsh environments, such as aerospace, where vibration and extreme temperatures are common.
- Prototyping Flexibility: One of the primary benefits of the board is its adaptability for rapid modifications, which makes it a valuable tool for engineers and hobbyists in the prototyping phase of circuit design.
- Environmental Resilience: It operates reliably in varying environmental conditions, such as temperature fluctuations and humidity, making it a trusted choice for both lab and field applications.
Summary:
The 589R112G01 Wire Wrap Board is an essential tool for engineers, hobbyists, and makers, offering a flexible, durable, and efficient platform for creating and testing electronic circuits. By utilizing wire wrapping, it eliminates the need for soldering, allowing for easy modifications during the prototyping phase. The board’s construction, using high-quality materials, ensures longevity and performance even under harsh conditions. With applications in aerospace, telecommunications, and industrial automation, the board remains versatile and adaptable to different sectors. As technology advances, improvements in wire wrap technology may further enhance its capabilities, ensuring its continued relevance in circuit design and development.
FAQs:
- What is the main advantage of using a wire wrap board like the 589R112G01 over traditional soldering?
- The main advantage is flexibility. Wire wrapping allows for easy adjustments and modifications to circuits without the need for desoldering. This makes it ideal for prototyping, where frequent changes to the circuit design are common.
- Can the 589R112G01 Wire Wrap Board handle high-frequency signals?
- Yes, it is designed to maintain a steady, low-impedance path, making it ideal for high-frequency and precision applications, where soldered connections might cause signal loss or interference.
- What industries use the 589R112G01 Wire Wrap Board?
- It is used in aerospace, telecommunications, industrial automation, and other sectors where reliable circuit connections are critical, particularly in environments subject to extreme conditions like vibration or temperature variations.
- How easy is it to modify circuits on the 589R112G01 Wire Wrap Board?
- Very easy. You can reconfigure connections quickly by unwrapping and rewrapping the wires, unlike soldered circuits that require desoldering for changes.
- What materials are used to construct the 589R112G01 Wire Wrap Board?
- The board is typically made of fiberglass or phenolic resin, known for their excellent mechanical strength and electrical insulation properties. The terminals are coated with protective metals like tin, silver, or gold to enhance durability and prevent corrosion.
- How do I maintain the 589R112G01 Wire Wrap Board?
- Regular maintenance involves checking for loose connections, cleaning the surface, and inspecting for potential short circuits to ensure long-lasting performance.
Read more about Accessories at Visit SearchKnowledge
Leave a Reply